介绍离心式通风机叶轮改进工艺
发布时间: 2016年02月22日
某种型号电机原配装的离心式通风机,经常出现叶轮损坏现象。维修时经检查发现叶轮出现故障较多的原因是,叶片疲劳点断裂使动平衡后配重块失去平衡作用。
叶轮损坏后增加了风机的维修量和备件的更换费用,严重时断裂的叶片还会飞入被冷却的主电机,从而造成主电机事故,有必要进行相关的技术改进。
1 叶轮改进前的状况
改进前的离心式通风机叶轮要求在φ290的圆周上,均匀安装56片厚度为2mm的圆弧形叶片,各叶片与轮盘、轮盖采用叶片两端自带的4个凸耳铆接而成。
改进前叶轮在铆接装配时需要注意:将叶轮两端的凸耳部分穿入轮盘、轮盖上相应的安装定位孔,在保证叶轮正确的旋向及各叶片与轮盘、轮盖的垂直度后,弯曲叶片两端的凸耳部分,将4个凸耳分别与轮盘、轮盖铆接紧密而成。
改进前叶轮装配出现的问题:
(1)叶片与轮盘、轮盖装配时,56个叶片与轮盘、轮盖的定位安装不易。装配时先将各叶片穿入轮盘上的安装孔,再将长度一致的各叶片逐一穿入轮盖上的孔。在穿入下一叶片时,经常发生因轮盖要轻微抬高而导致将已穿好的叶片从孔中脱出的现象;
(2)各叶片与轮盘、轮盖的垂直度不易调整保证。因叶片两端的凸耳在铆接时扣倒方向一致,常会发生轮盖向一个方向旋扭倾斜现象;
(3)叶片、轮盘、轮盖所用材质料厚均较薄,动平衡时所采用的增重平衡块只能卡装在叶片上。由于装配该风机的主电机时环境比较恶劣,有的在沙漠,有的在湿地,均为露天作业。蚊虫、灰尘、雨水经常被吸入,粘附在叶轮上。由于叶轮叶片过密,粘附物不易完全清除,易使叶轮动平衡被破坏;
2 叶轮的技术改进
因该型通风机外形小巧,在主电机上安装时占用的空间位置不大,用户对此比较认可。所以在改进时保留了原通风机的蜗壳组件、进风口组件及进气箱,重点针对叶轮进行了重新核算设计,以消除原叶轮存在的缺陷。
设计改进时保证了以下几点:
(1)新叶轮的宽度≤原叶轮的宽度,以保证叶轮与进风口的安全距离;
(2)新叶轮的外径≤原叶轮的外径,保证能顺利安装;
(3)新叶轮叶片数量少于原叶轮叶片的数量,加工工艺性能优于原叶轮的工艺性能(必须利于各配件的加工成型及叶片与轮盘、轮盖的总装);
(4)整体叶轮的强度、刚度大于原叶轮,同时满足风机运行所必须的安全系数;
(5)配装新叶轮风机的空气动力性能优于装配原叶轮的风机。
综合以上各点要求,进行详细的分析、计算与理论验证,以保证新设计叶轮的安全可靠性和空气动力性能。
该叶轮采用了32个叶片(其中加强型叶片4个,常规叶片28个),各叶片与轮盖、轮盘的接合部位均要求满焊。同时将各叶片厚度增加到3mm,轮盘厚度增加到5mm,轮盖的厚度增加到4mm。叶轮装配改进后,各配件自身的强度增大,保证了焊接组件结构的稳定性和运行的可靠性。
为保证焊接时各叶片与轮盘、轮盖的垂直度以及在圆周上的均布等分,制作了一套焊接工装。因叶片数量减少,各叶片与轮盘、轮盖间可顺利实施满焊。焊接时采取工艺措施,防止叶轮的焊接变形。叶轮动平衡时所增加的平衡块要焊牢在轮盘、轮盖内侧的相应位置。
3 叶轮改进前后对比分析
新叶轮焊接制出后,将原风机的蜗壳、进风口及进气箱,与原型号风机装配在一起,然后在主电机上安装、在相同试验条件的工况下做对比试验。两种叶轮所装配的风机在相同工况下运行测试的性能指标。
从试验结果来看,安装改进后叶轮的离心通风机效果更好。被冷却电机的主极温升、副极温升、电枢温升,比安装原叶轮离心式通风机时有明显降低,且通风机电机运行电流较低,在持续作业的工作状况下,风机电机不易过电流。
4 生产应用
在改进型叶轮试验成功后,已停止进行原叶轮的生产。现装配于主电机的离心式通风机均配装了改进型叶轮,不仅消除了原叶轮存在的安全隐患,同时使通风机的空气动力性能也有了较大幅度的提高。
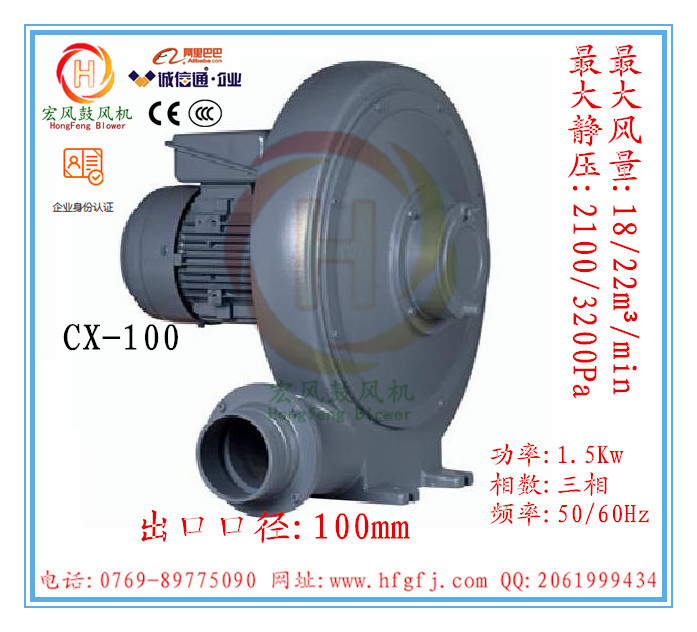
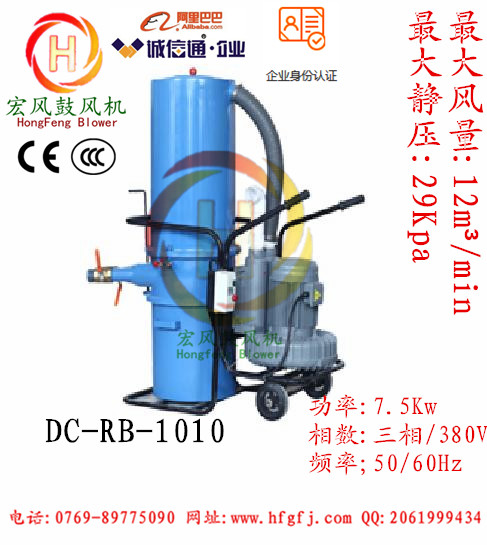
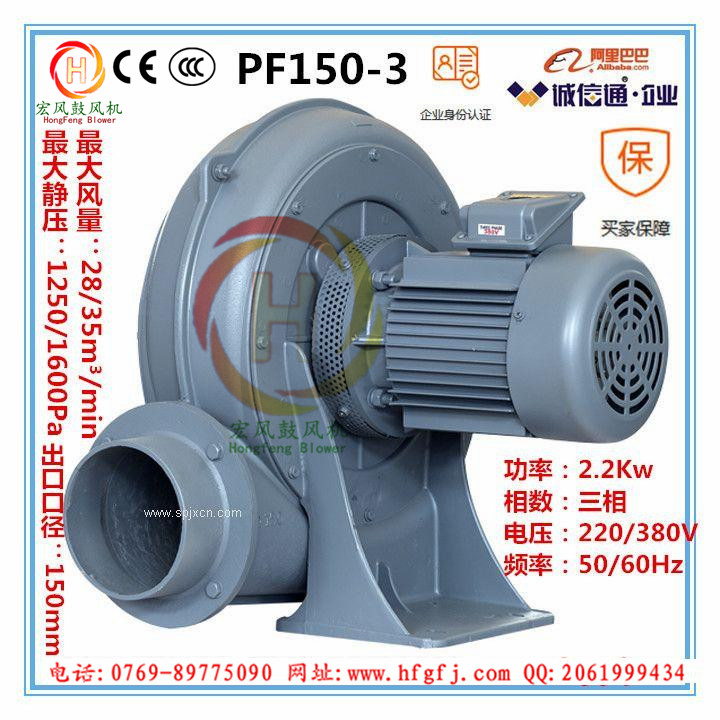
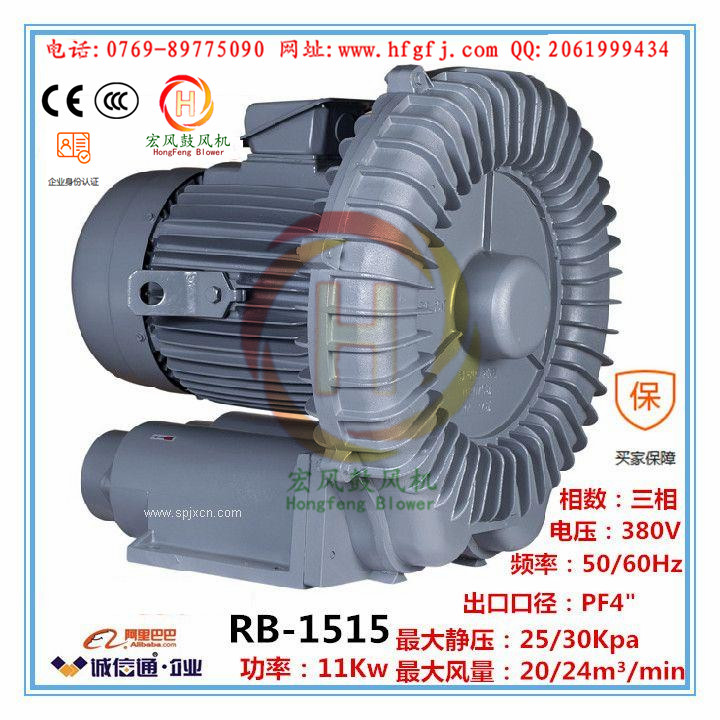
叶轮损坏后增加了风机的维修量和备件的更换费用,严重时断裂的叶片还会飞入被冷却的主电机,从而造成主电机事故,有必要进行相关的技术改进。
1 叶轮改进前的状况
改进前的离心式通风机叶轮要求在φ290的圆周上,均匀安装56片厚度为2mm的圆弧形叶片,各叶片与轮盘、轮盖采用叶片两端自带的4个凸耳铆接而成。
改进前叶轮在铆接装配时需要注意:将叶轮两端的凸耳部分穿入轮盘、轮盖上相应的安装定位孔,在保证叶轮正确的旋向及各叶片与轮盘、轮盖的垂直度后,弯曲叶片两端的凸耳部分,将4个凸耳分别与轮盘、轮盖铆接紧密而成。
改进前叶轮装配出现的问题:
(1)叶片与轮盘、轮盖装配时,56个叶片与轮盘、轮盖的定位安装不易。装配时先将各叶片穿入轮盘上的安装孔,再将长度一致的各叶片逐一穿入轮盖上的孔。在穿入下一叶片时,经常发生因轮盖要轻微抬高而导致将已穿好的叶片从孔中脱出的现象;
(2)各叶片与轮盘、轮盖的垂直度不易调整保证。因叶片两端的凸耳在铆接时扣倒方向一致,常会发生轮盖向一个方向旋扭倾斜现象;
(3)叶片、轮盘、轮盖所用材质料厚均较薄,动平衡时所采用的增重平衡块只能卡装在叶片上。由于装配该风机的主电机时环境比较恶劣,有的在沙漠,有的在湿地,均为露天作业。蚊虫、灰尘、雨水经常被吸入,粘附在叶轮上。由于叶轮叶片过密,粘附物不易完全清除,易使叶轮动平衡被破坏;
(4)风机在连续工作制的运行状态下,叶轮由于在外界因素所造成的不平衡状态下长时间运行,会使叶片在达到疲劳极限后,从两端铆接处的凸起部位撕裂,发生故障。
2 叶轮的技术改进
因该型通风机外形小巧,在主电机上安装时占用的空间位置不大,用户对此比较认可。所以在改进时保留了原通风机的蜗壳组件、进风口组件及进气箱,重点针对叶轮进行了重新核算设计,以消除原叶轮存在的缺陷。
设计改进时保证了以下几点:
(1)新叶轮的宽度≤原叶轮的宽度,以保证叶轮与进风口的安全距离;
(2)新叶轮的外径≤原叶轮的外径,保证能顺利安装;
(3)新叶轮叶片数量少于原叶轮叶片的数量,加工工艺性能优于原叶轮的工艺性能(必须利于各配件的加工成型及叶片与轮盘、轮盖的总装);
(4)整体叶轮的强度、刚度大于原叶轮,同时满足风机运行所必须的安全系数;
(5)配装新叶轮风机的空气动力性能优于装配原叶轮的风机。
综合以上各点要求,进行详细的分析、计算与理论验证,以保证新设计叶轮的安全可靠性和空气动力性能。
该叶轮采用了32个叶片(其中加强型叶片4个,常规叶片28个),各叶片与轮盖、轮盘的接合部位均要求满焊。同时将各叶片厚度增加到3mm,轮盘厚度增加到5mm,轮盖的厚度增加到4mm。叶轮装配改进后,各配件自身的强度增大,保证了焊接组件结构的稳定性和运行的可靠性。
为保证焊接时各叶片与轮盘、轮盖的垂直度以及在圆周上的均布等分,制作了一套焊接工装。因叶片数量减少,各叶片与轮盘、轮盖间可顺利实施满焊。焊接时采取工艺措施,防止叶轮的焊接变形。叶轮动平衡时所增加的平衡块要焊牢在轮盘、轮盖内侧的相应位置。
3 叶轮改进前后对比分析
新叶轮焊接制出后,将原风机的蜗壳、进风口及进气箱,与原型号风机装配在一起,然后在主电机上安装、在相同试验条件的工况下做对比试验。两种叶轮所装配的风机在相同工况下运行测试的性能指标。
从试验结果来看,安装改进后叶轮的离心通风机效果更好。被冷却电机的主极温升、副极温升、电枢温升,比安装原叶轮离心式通风机时有明显降低,且通风机电机运行电流较低,在持续作业的工作状况下,风机电机不易过电流。
4 生产应用
在改进型叶轮试验成功后,已停止进行原叶轮的生产。现装配于主电机的离心式通风机均配装了改进型叶轮,不仅消除了原叶轮存在的安全隐患,同时使通风机的空气动力性能也有了较大幅度的提高。
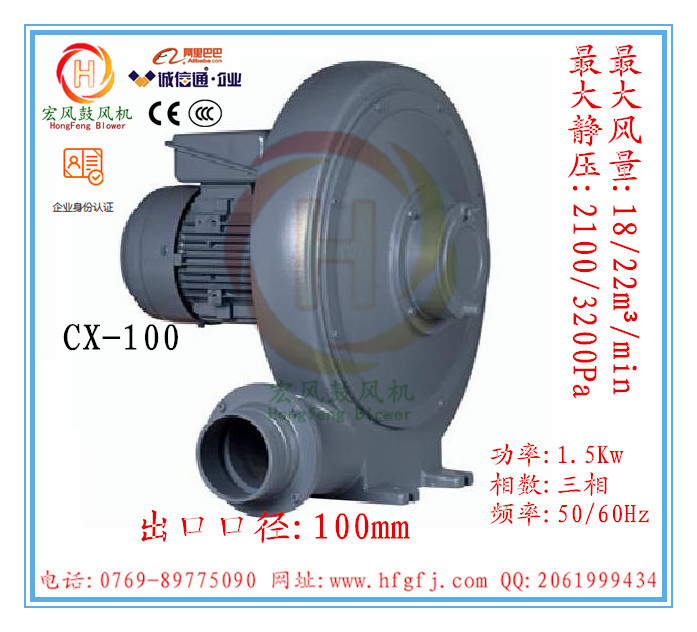
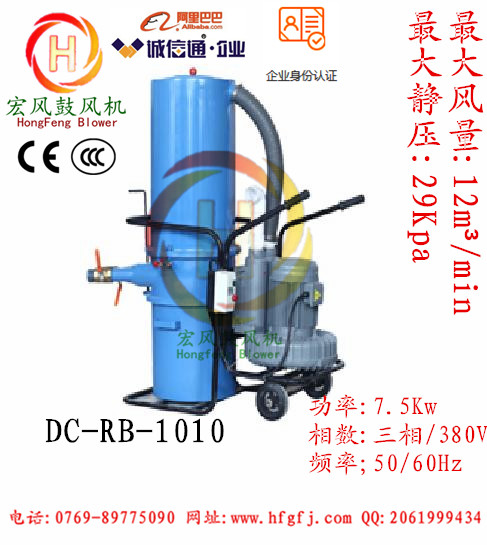
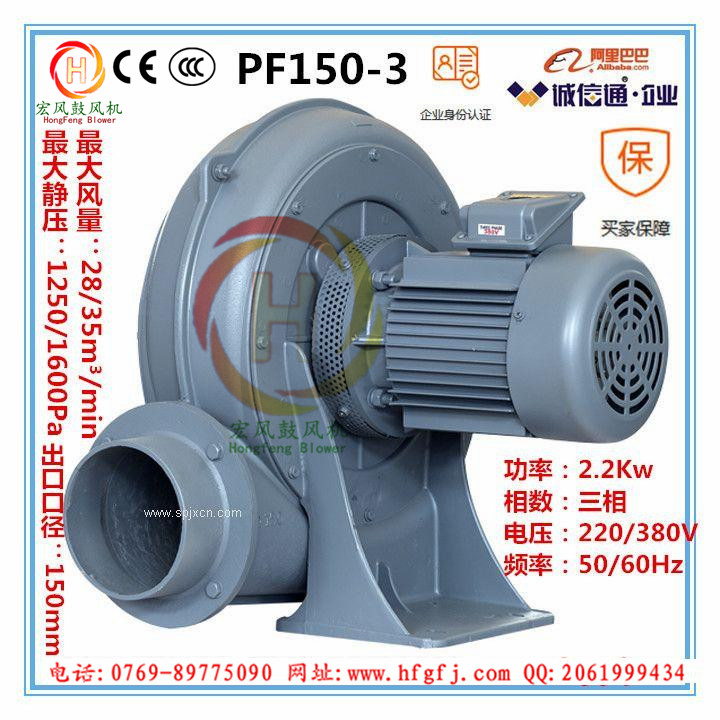
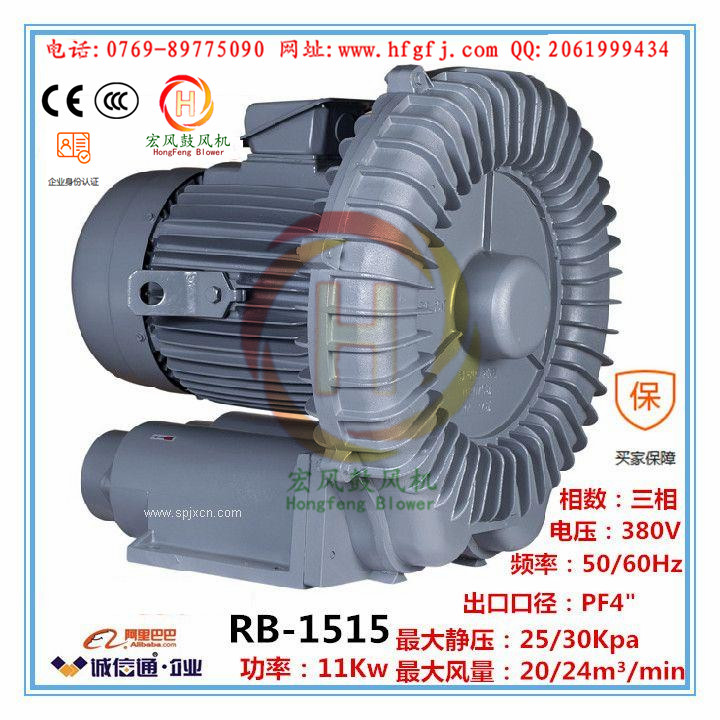
上一篇新闻:根据鼓风机外形特点选风机下一篇新闻:选择好风机的简单知识要领